Discover the Best Practices for Effective Foam Control in Industrial Applications
Discover the Best Practices for Effective Foam Control in Industrial Applications
Blog Article
A Comprehensive Overview to Executing Foam Control Solutions in Your Operations
Effective foam control is a vital facet of operational performance that usually goes forgotten. Recognizing the details of foam generation can dramatically affect both efficiency and product quality. By examining key variables such as application compatibility and employees training, companies can enhance their foam management initiatives.
Recognizing Foam Difficulties
Foam difficulties are a significant concern across numerous sectors, influencing operational effectiveness and product top quality. The development of too much foam can impede processes such as mixing, transport, and storage, resulting in enhanced downtime and waste. In sectors like food and beverage, pharmaceuticals, and petrochemicals, foam can interfere with production lines, causing item incongruities and contamination threats.
In addition, foam can obstruct equipment capability, resulting in costly fixings and upkeep. In wastewater therapy, foam can disrupt clarifier procedures, resulting in lower treatment efficiency and regulatory compliance issues.
Comprehending the underlying sources of foam generation is important for effective monitoring. Variables such as surfactants, temperature fluctuations, and anxiety levels can all add to foam manufacturing. Determining these aspects allows industries to carry out targeted strategies that reduce foam development while keeping item integrity.
Sorts Of Foam Control Solutions
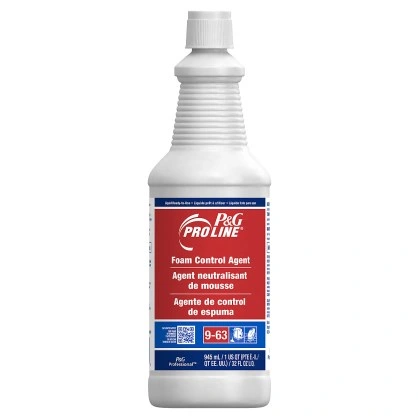
Mechanical remedies involve the use of devices such as foam skimmers or defoamers. Chemical services, on the other hand, include the application of defoaming representatives-- compounds that interfere with the foam framework, leading to its collapse. Foam Control.
Lastly, operational techniques concentrate on procedure adjustments. This may entail changing devices specifications, such as temperature and stress, or changing the flow rates of fluids to lessen foam generation. In addition, applying great housekeeping practices can also alleviate foam development by decreasing pollutants that add to foam security.
Choosing the proper foam control option includes examining the certain requirements of the operation, including the kind of procedure, the features of the materials involved, and safety considerations.
Selecting the Right Products
Choosing the right foam control items calls for a thorough understanding of the specific application and its distinct challenges. Elements such as the kind of foam, the atmosphere in which it happens, and the desired end result all play essential functions in item option. Foam Control. For example, in markets such as food handling, it is vital to select food-grade defoamers that abide by safety laws while successfully managing foam.
Furthermore, consider the thickness of the fluid where the foam problem exists. Some items are developed for low-viscosity applications, while others are customized for other thicker fluids. Compatibility with existing processes is an additional important facet; the selected foam control agents need to integrate perfectly without interfering with overall procedures.
An additional vital variable is the method of application. Some products might require dilution, while others can be applied straight. Evaluating the ease of use and the called for dose can supply understandings right into the product's performance and cost-effectiveness.
Application Techniques
Effective execution strategies for foam control services need an organized strategy that aligns product selection with operational requirements. The initial step includes a thorough analysis of the processes where foam happens, determining certain locations that demand intervention. By involving cross-functional groups, including manufacturing, design, and quality assurance, organizations can gather insights that educate the selection of the most effective foam control items.
Following, it is vital to develop clear goals for foam reduction, making sure that these goals are possible and quantifiable. This may involve defining appropriate foam degrees and the timelines for application. Training employees on the residential properties and application techniques of chosen foam control agents is similarly essential, as appropriate use is important for ideal results.
Furthermore, incorporating foam control solutions right into existing workflows needs mindful preparation. Ultimately, a well-structured technique will boost operational effectiveness while properly managing foam-related difficulties.
Tracking and Evaluating Efficiency
Monitoring and examining the effectiveness of foam control services is crucial for making sure that applied methods produce the wanted results. This process involves organized information collection and analysis to assess the performance of foam control agents and techniques. Key performance indicators (KPIs) must be developed before execution, More hints allowing for a clear baseline versus which to determine development.
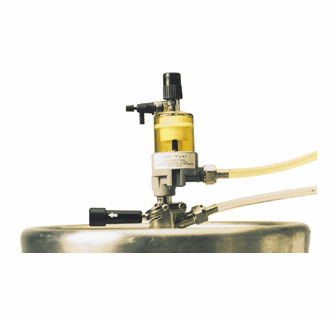
Examining efficiency additionally calls for routine testimonials of foam control treatments and representative efficiency. This can be completed via tasting and screening, enabling operators to identify if present services are meeting operational needs. It is essential to solicit feedback from group participants who communicate with these systems daily, as their insights can reveal functional subtleties that measurable data might forget.
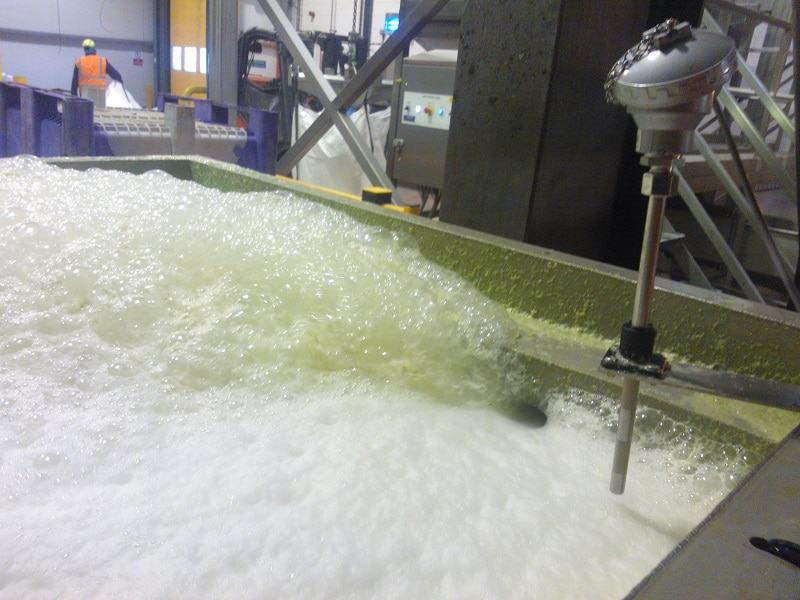
Inevitably, a structured monitoring and examination structure aids identify needed changes, ensuring that foam control solutions stay reliable, cost-efficient, and lined up with organizational objectives.
Verdict
In verdict, efficient foam control services are vital for optimizing functional performance and preserving product top quality. A thorough understanding of foam obstacles, integrated have a peek here with the selection of ideal items and application techniques, facilitates the effective administration of foam generation. Developing quantifiable KPIs and investing in employees educating even more improve the performance of foam control actions. Normal monitoring and evaluation guarantee continuous improvement, ultimately leading to a much more structured and effective operational atmosphere.
Implementing excellent housekeeping techniques can also alleviate foam formation by reducing impurities that add to foam security.
Selecting the right foam control products needs a complete understanding of the specific application and its distinct difficulties (Foam Control).Effective execution strategies for foam control services need a methodical strategy that aligns product choice with functional demands.In verdict, effective foam control services are necessary for maximizing operational efficiency and maintaining product top quality. A thorough understanding of foam difficulties, incorporated with the option of appropriate products and implementation techniques, assists in the effective monitoring of foam generation
Report this page